在喇叭智能化与个性化需求井喷的今天,车载、头戴式、蓝牙喇叭作为用户体验的核心部件,其生产模式正面临严峻挑战。传统制造工艺依赖单一型号,大批量生产难以应对多品种、小批量的市场需求,且人工操作易导致效率低下、良率波动、装配精度不足等问题。如何实现高效、高质、灵活的生产?星特科技电声柔性半自动生产线应需而生,以创新技术成为喇叭行业制造升级的关键。
随着喇叭行业的不断发展,电声制造领域正面临前所未有的生产挑战与技术压力。传统的喇叭生产线往往只能适应单一型号的生产,换产周期长,成本高,且在生产过程中难以保证产品的一致性和良率。此外,随着3C、汽车行业智能化普及,喇叭的需求也向高保真、轻量化、多功能集成方向演进,这对生产设备和技术提出了更高的要求。星特科技深耕喇叭自动化领域,针对以上喇叭行业痛点,推出UPH 1500-1650Pcs、良率98%的柔性半自动产线,以四大核心技术模块,助力客户突破生产瓶颈,构建差异化竞争力。智能点胶与AOI检测:通过A/B点胶解决方案与AOI视觉系统,胶量误差从传统±20%降低至±1%~2%,彻底解决溢胶、缺胶问题,效率提升3-5倍。双重定位保障:采用双重AOI纠偏检测与高度检测技术,PCB板偏位精度控制在±0.1%,确保后续工序零缺陷流转。视觉引导调音网贴合:星特采用500W像素彩色CCD视觉系统实时检测,调音纸贴合精度达0.03mm,杜绝偏位与高度不均。UV固化与引线整形:UV光源功率自适应调节,同步完成引线预固化;自动整形技术搭配3D线扫相机检测音圈引线空间位置,确保引线符合工艺标准,提高产品良率。机械手与翻转机构协同:真空吸附与弹性支撑设计,避免治具卡位;伺服驱动倒模机实现快速扣合,CT时间大幅缩短。合膜精度保障:正向治具与翻转平台精密配合,确保膜片组装无损伤、无偏差。视觉引导点焊:1200万像素彩色CCD定位焊接,精度±0.05mm,保压测高精度±0.05mm,解决传统焊接效率低、良率波动的难题。
多功能集成:双轴机械手与三轴移动平台灵活适配裁线、拔线、测阻抗、极性检测等工序,满足复杂工艺需求。
智能充磁技术:高精度充磁台通过自动化控制,磁化强度均匀性显著提升,保障BL值稳定,产品性能一致性达行业领先水平。
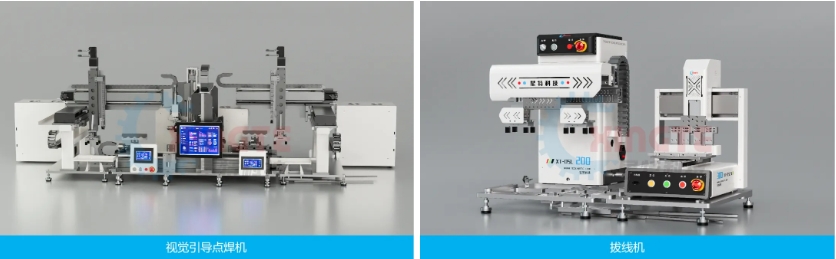
星特科技电声柔性半自动线不仅实现了生产效率与品质的双重突破,更通过模块化设计支持快速换产,适配多型号生产需求。未来,随着AI工艺优化、AR运维、人机协作等技术的深度融合,产线将向智能化、数字化纵深发展,为高保真、轻量化喇叭等新兴需求提供前瞻性解决方案。
星特科技始终以客户为中心,通过技术创新与全球化交付能力,助力电声制造企业打破内卷困局,抢占智能化时代的市场先机。